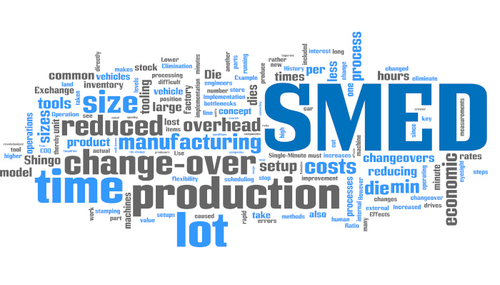
Projet SMED Emboutissage
Voici l’exemple d’un projet SMED qui nous a permis de réduire de 90% le temps de changement d’outils sur une presse tandem d’emboutissage.
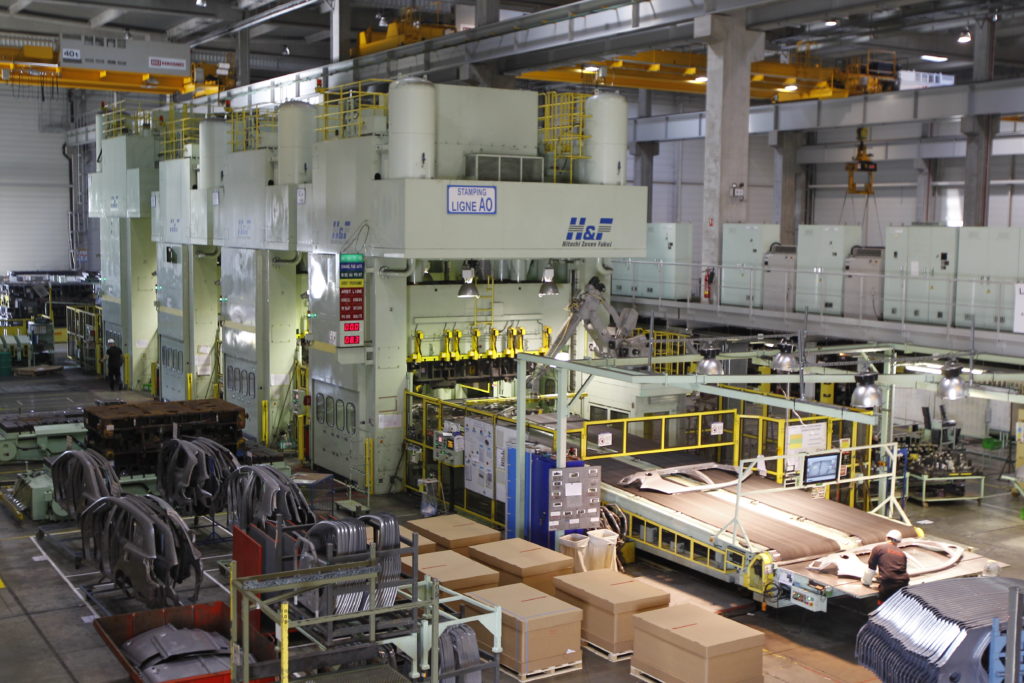
Rappel rapide : qu’est ce que le SMED (single minute exchange die)
Je rappelle brièvement les grandes phases de la méthode :
Standardiser les opérations
Séparer les taches internes (effectués dans la machine à l’arrêt) des taches externes (pouvant être effectués pendant la production).
Transformer des actions internes en externe.
Rationnaliser les actions.
Ordonnancer les actions.
Création d’un nouveau standard.
Mesurer les résultats.
Et on recommence jusqu’à atteindre notre objectif.
Pour plus de détails je vous invite à visiter l’article si joint : https://orangestrategie.com/article-2-le-smed-single-minute-exchange-die/
Etape 1 : Séparation taches internes et externes
Dans le cas présent, à l’état initial : le changement des outils demande 70 minutes d’arrêt de production.
Lors de l’étape 1, on a recherché de séparer simplement les taches Internes / externes. Nous avons donc commencé par gagner du temps sur la manipulation des outils : en mettant sur la presse un bolster à 2 positions. Ceci nous permet donc de positionner nos outils sur un poste à vide mobile à côté de la presse. Nous avons appliqué la même solution pour le changement des piles de flancs. Nous avons donc obtenu un gain de 32 minutes, soit 45% du temps de set-up.
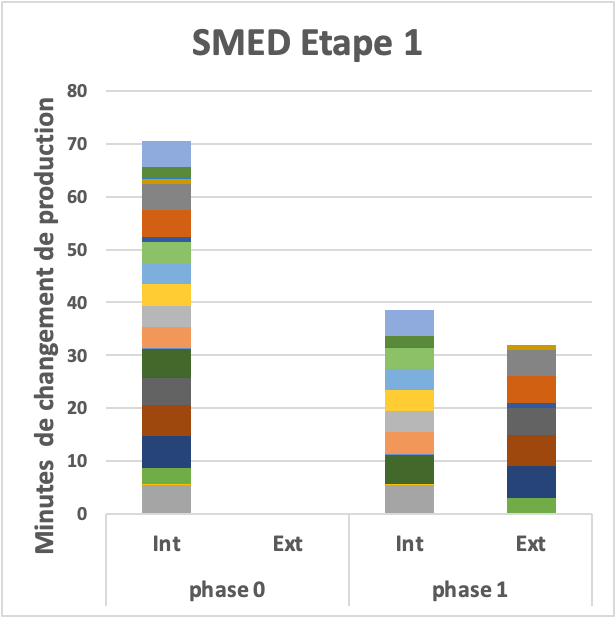
Etape 2 : optimisation taches internes avec bridge automatique des outils
Ici pour gagner du temps interne, nous avons automatisé les opérations de bridage et débridage des outils, qui sont vraiment chronophage.
Nous avons donc réduit le set-up de 10 minutes.
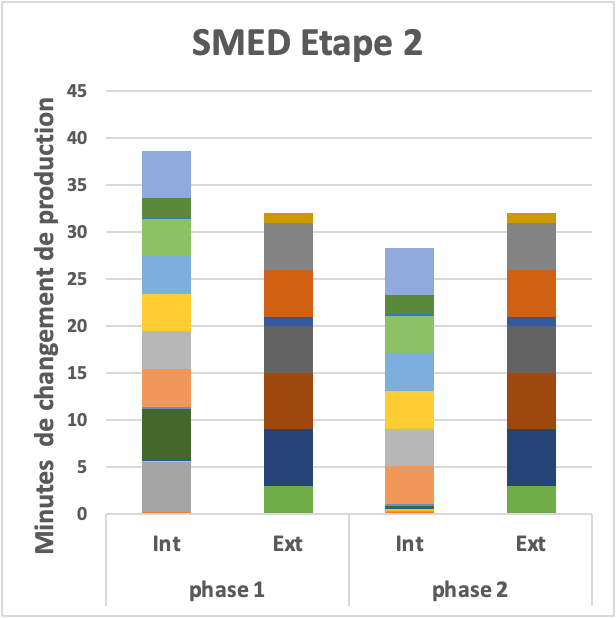
Etape 3 : préparation du changement des préhenseurs inter-presses
Le changement des préhenseurs de pièce en très les presses est une opération interne, par contre on peut gagner du temps avec une phase de préparation qui mettra les préhenseurs au plus près de la zone robot. De plus en mettant un système de montage rapide sur le robot, on réduit le temps d’installation des préhenseurs.
Nous gagnons donc 14 minutes de set-up. Nous arrivons donc à un set up de 14,4 minutes.
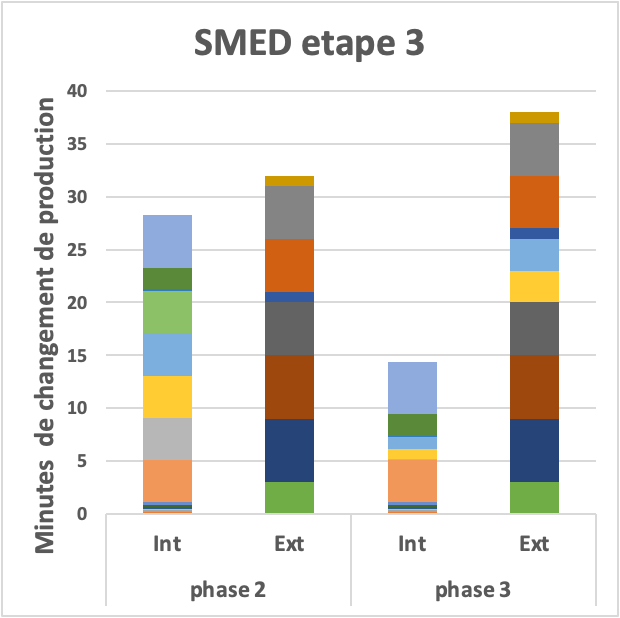
Etape 4 : optimisation de l’organisation pour le contrôle outils et 1ière pièce
Nous sommes arrivés à un set-up de 14 min, et nous pouvons encore le réduire en travaillant sur l’organisation des tâches.
Le contrôle des outils dans la presse avant le démarrage de production est un temps incompressible par outil. Mais nous pouvons contrôler tous les outils en même temps en utilisant les opérateurs de sortie de presse, à condition de les former à cette tache.
De plus nous contrôlons la première pièce avant de lancer la production. Il est tout à fait possible de de faire ce contrôle une fois la production démarrée en transférant cette tache au Team Leader.
Ceci fait, nous arrivons à un set-up de 6,4 minutes.
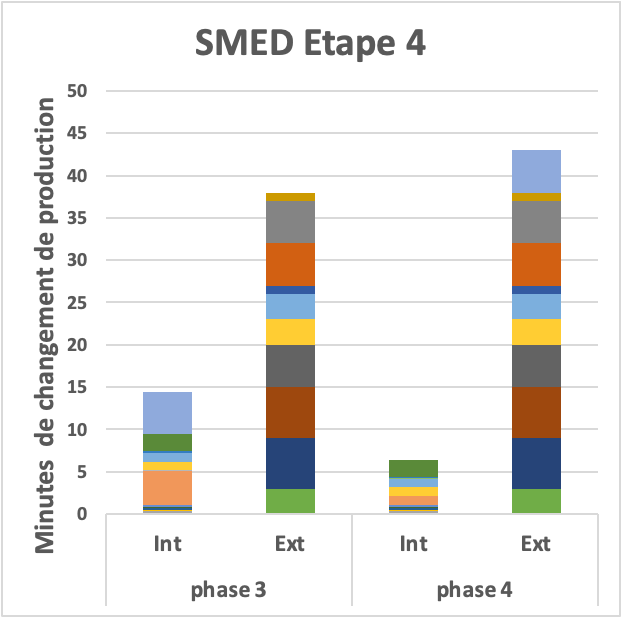
Etape 5 : Réduction du temps de préparation pendant la production
Alors que nous avons réduit le temps set-up, nous avons augmenté le temps des taches extérieures, donc le temps de préparation de production.
La réduction du temps de set-up nous permet de réduire les tailles de lot des productions. Mais nous sommes confrontés au problème suivant : les tailles de lots doivent être suffisamment importantes pour couvrir le temps de préparation de production, que nous venons d’augmenter.
Il faut donc maintenant réduire le temps de préparation afin de continuer la réduction des tailles de lot.
Nous pouvons réduire le temps de préparation de 43 à 17,5 minutes avec plusieurs kaizen :
Free-location des outils pour limiter les temps de déplacement du pont roulant à vide.
Installer un viseur laser sur le pont pour faciliter le positionnement des outils sur son bolster.
Ranger les préhenseurs sur leurs outils pour réduire les déplacements.
Préparation des palettes de flancs par le cariste logistique et non le pilote de la presse.
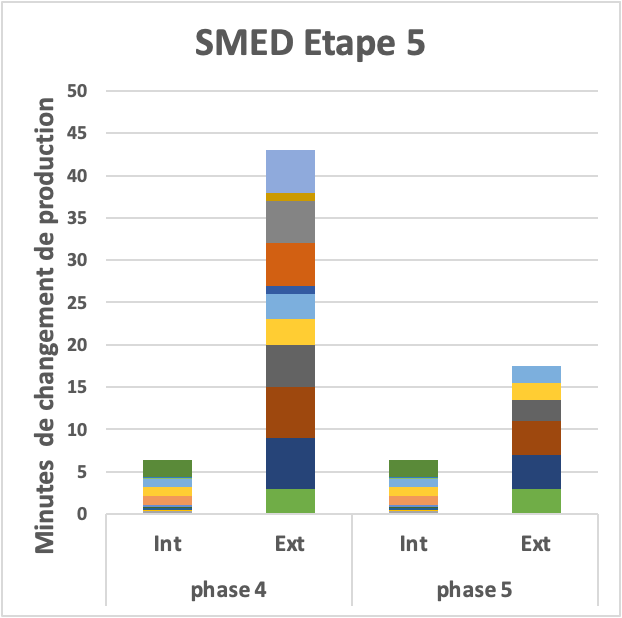
Conclusion :
Avec les différents kaizen mis en place, nous avons réussi à réduire de 90% le temps de changement de production sur cette ligne de presse. Ceci nous a donc permis de réduire nos tailles de lots de 90% aussi . Cela a donc un impact énorme sur la quantité et la valeur du stock de pièces embouties. Cette méthodes SMED est donc indispensable pour réduire nos stocks et « tendre » notre flux de production. C’est la base pour mettre en place la production en juste à temps.
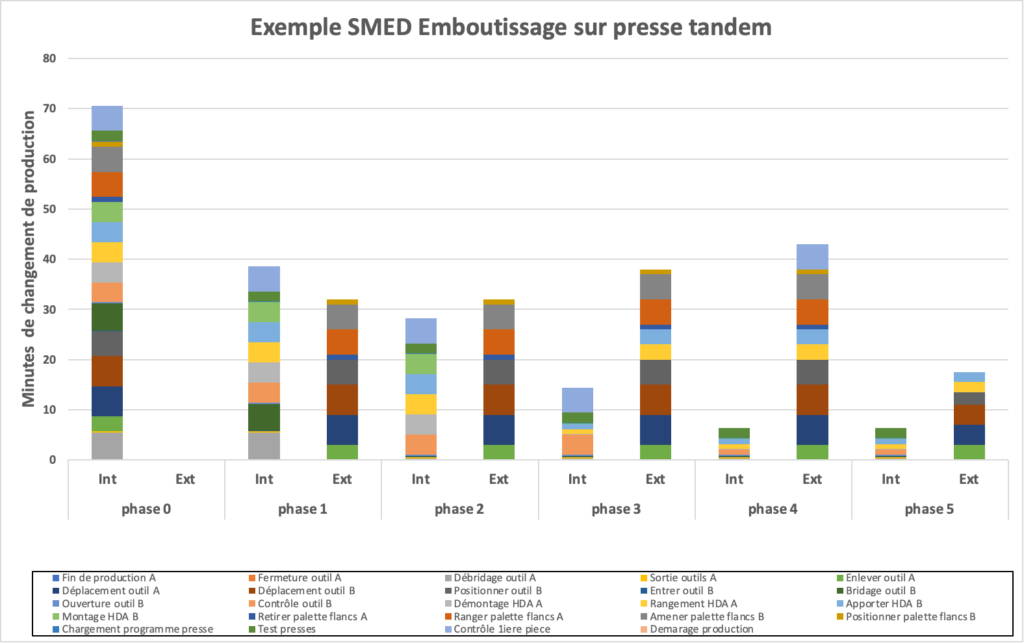