Ce projet a pour objectif de réduire la consommation en gaz de la ligne de peinture cataphorèse, sans faire d’investissement. Nous allons donc voir quelles sont les opportunités de Kaizen que nous pouvons mettre en place.
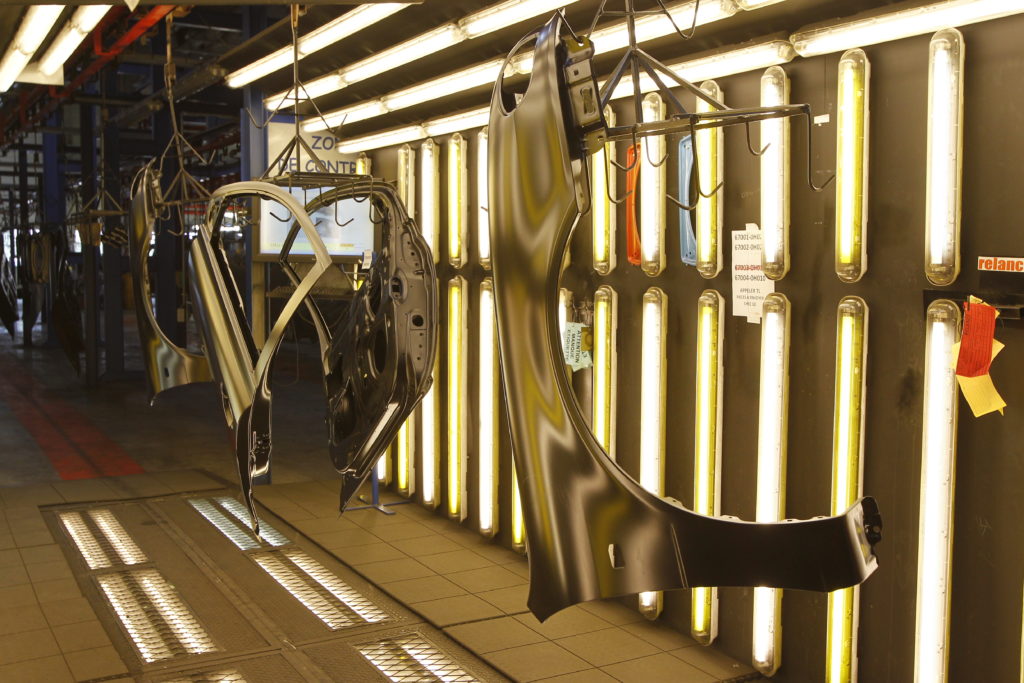
Description de la ligne
La ligne de peinture par cataphorèse est schématisée ci-dessous :
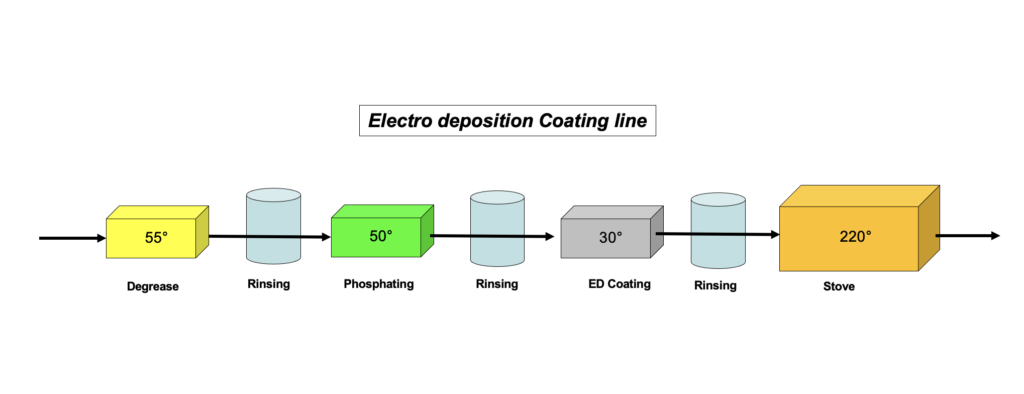
Nous accrochons les pièces à peindre sur convoyeur aérien qui va transporter les pièces dans les process suivants :
Dégraissage dans 2 bains à 55°
Rinçage
Phosphatation dans un bain à 50°
Rinçage
Dépôt de peinture par électrodéposition dans un bain à 30°
Rinçage
Cuisson de la peinture dans une étuve à 220°
Il reste plus qu’à décrocher les pièces pour le conditionnement.
Cette ligne de peinture produit en 2 équipes 5 jours par semaine.
Ici ce qui nous intéresse, c’est de réduire la consommation du gaz qui sert à chauffer les différents bains et l’étuve de cuisson. Cela représente la majeure quantité d’énergie consommée par la ligne de cataphorèse. Voici une représentation de la consommation sur une semaine :
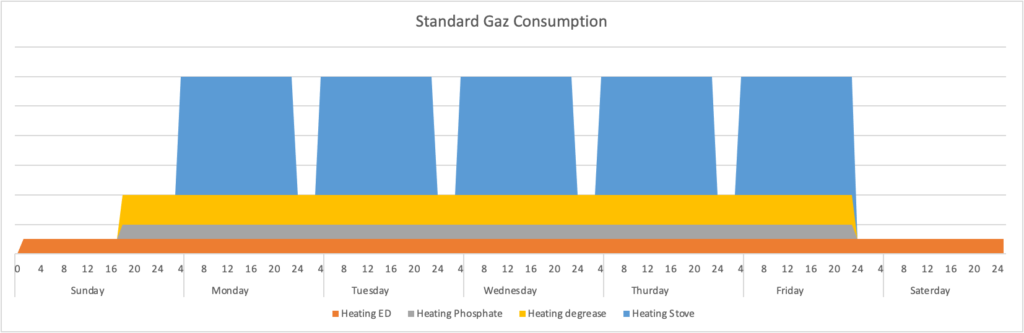
Optimisation de fonctionnement
Le premier Kaizen, facile à réaliser : c’est de retarder le démarrage de la chauffe des bains du dimanche après-midi.
Le standard nous demande de démarrer la chauffe le dimanche à partir de 17H, afin que l’installation soit en température le lundi matin à 5H pour le démarrage de la production. Nous pouvons retarder la mise en chauffe des bains de 4H le dimanche à condition que les échangeurs thermiques soient propres. Donc pour faire ce Kaizen nous décidons de changer la fréquence de nettoyage des échangeurs thermique de la dégraisse et de la phosphate. C’est bon, nous avons donc gagné 1% de consommation de gaz.
Le deuxième Kaizen, ne nous coûte rien, il suffit juste d’appliquer le principe de base du TPS : le juste à temps ou le juste nécessaire.
Initialement pour démarrer la production, il faut que tous les bains et l’étuve soient à la bonne température, alors on peut accrocher les premières pièces. Nous avons donc programmé les différentes chauffes pour être prêt le matin à 5H et nous arrêtons à la fin de la production. C’est une évidence.
Changement de raisonnement : les bains et l’étuve doivent être à la bonne température seulement quand la première pièce entre dans le process ; et on peut arrêter dès que la dernière pièce sort du process. Ceci nous fait gagner le temps du convoyage des pièces, soit environ 2H30 par jour. C’est évident comme kaizen et le gain est énorme : -7,5% sans rien faire!!!
Le troisième Kaizen, plus difficile, mais ne coute rien non plus : il faut juste baisser la température de cuisson des pièces.
La température de cuisson dépend du temps en température, comme on peut le voir sur cet abaque :
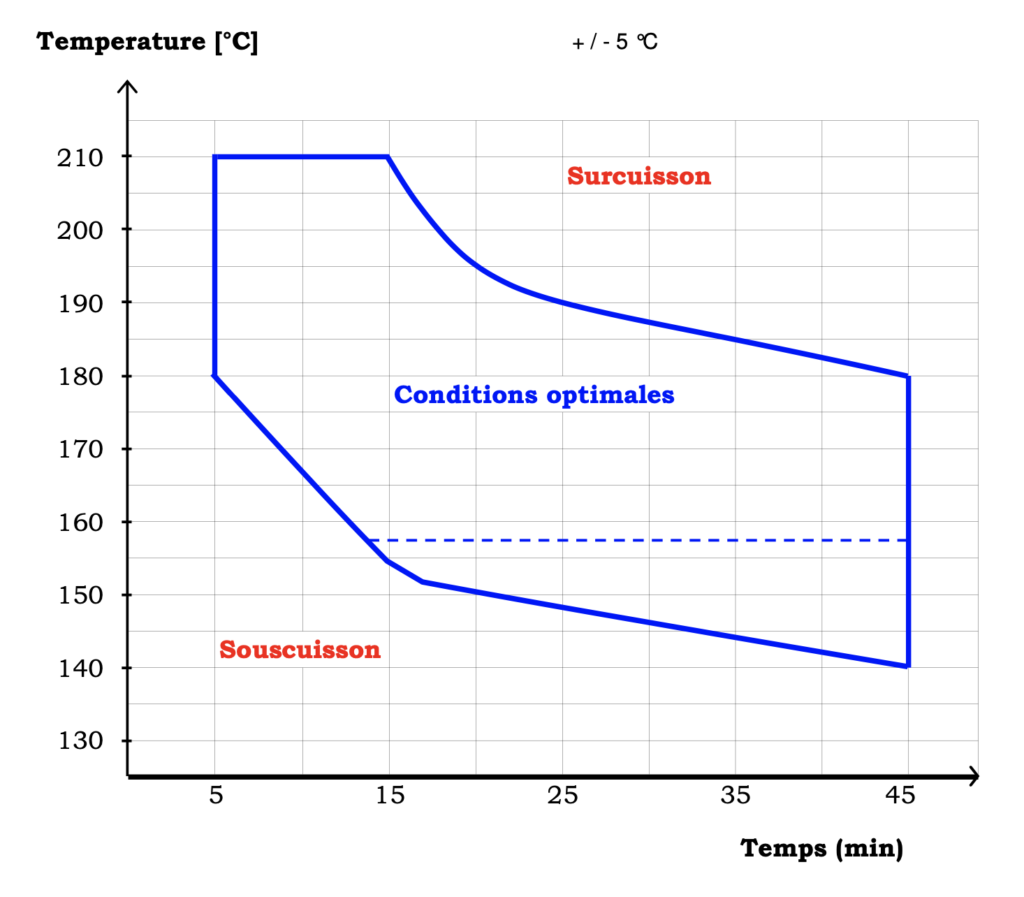
Dans notre situation, nous cuissons à la température maximum (210°) car les pièces ne restent pas longtemps dans l’étuve. Et en plus comme le résultat qualité nous satisfaisait, tout aller très bien comme cela.
Nous allons donc baisser la température de cuisson de 40°. Pour cela il faut que les pièces passent plus de temps dans l’étuve. Nous allons donc réduire la vitesse du convoyeur de 3m/min à 2,5m/min.
Pour réussir cette réduction de vitesse, il faut donc faire des kaizen d’accrochage pour ne pas perdre de la capacité de production qui nous obligerait de faire des heures supplémentaires (perte de tous les gains d’énergie).
Après validation qualité de la tenue et aspect peinture, après la réorganisation de l’accrochage et décrochage, la baisse de température de l’étuve nous a donc permis d’économiser 12% de consommation de gaz.
Il suffit maintenant de cumuler les différents kaizen et nous obtenons une réduction de 20% de la consommation de gaz.
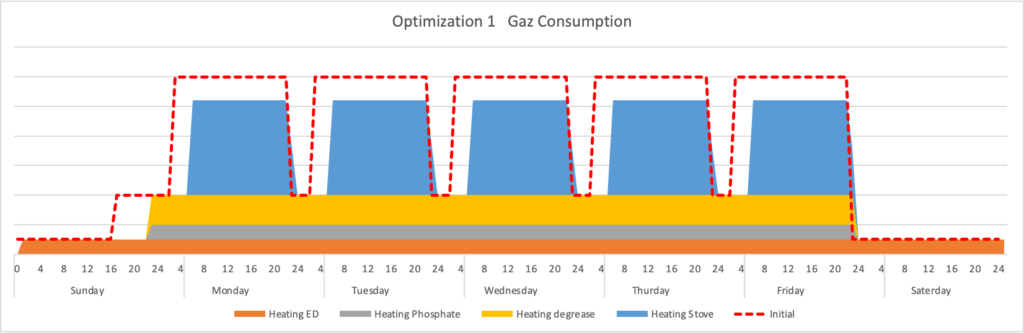
Optimisation de l’organisation de production
Maintenant, si nous voulons aller plus loin dans la réduction de la consommation de gaz, il faut explorer les voies de l’organisation des heures de production.
La première piste qui nous vient à l’esprit est de faire tourner la peinture sur 4 jours seulement, mais la perte de capacité de production n’est pas envisageable. Par contre nous pouvons nous contenter de travailler sur 4,5 jours par semaine avec les volumes actuels. Ceci nous ferait gagner 5% d’économie en plus, soit 25% au total.
Pour cela il faut réorganiser les horaires ou les taches de l’équipe de peinture en les affectant à d’autre taches.
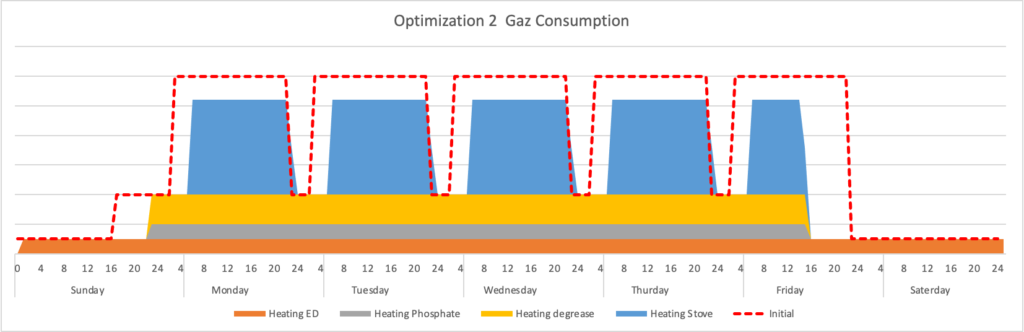